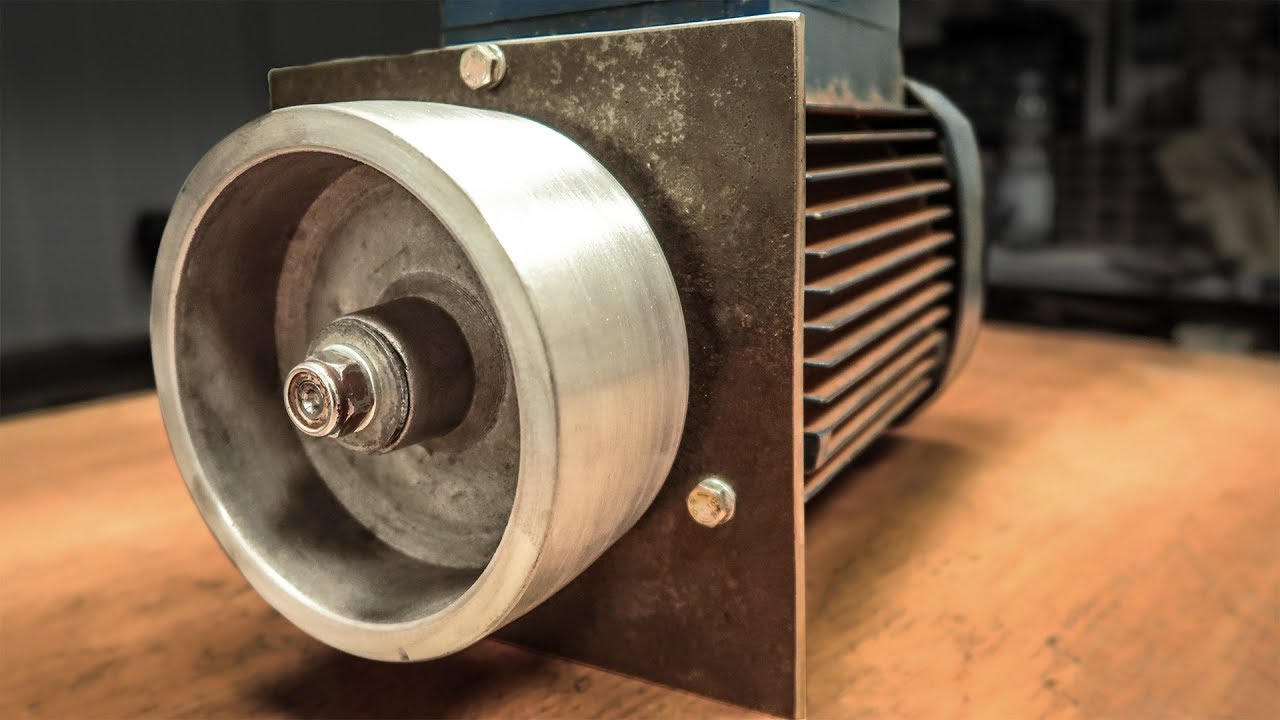
Just a little disclaimer:
Of course this is not the best motor for a belt grinder.
Of course this is not the best way to make a drive wheel and for sure it's also not the safest method to turn a true wheel on a motor.
This is just my own way of doing it, I just want to have fun and experiment with tools limitations to prove it can be done with decent results.
Fun fact:
This drivewheel runs more true than the one I have mounted on the 2x72 belt grinder. And that was turned on the lathe! (mind you, turned by me, so it's no surprise)
I just started to list some of the stuff I use for my projects in this amazon storefront:
https://www.amazon.com/shop/blackbear...
It's affiliate marketing, so if you order something from here you'll help the channel for free! Thank you!
Index of operation and materials:
0:37 This part needs to be shortened to expose more shaft
1:26 Clean up the cuts with 2x72 belt grinder
1:44 6mm thick steel mounting plate cut with angle grinder
2:09 Rough mark of mounting holes with spray can
2:20 Mark and center punch precise hole locations
2:40 Drill holes for bolts
3:25 Spacers needed to mount the motor securely
3:52 Mark position of shaft hole
4:00 Drill shaft hole
4:53 Design drive wheel pattern in Fusion360
Tip: Always add drafts to the walls of your pattern.
Note: Casting a true hole is hard, even with drafts!
5:08 3D print in PLA
5:20 Clean the pattern with box cutter and sandpaper, the smoother the better
5:44 Talc powder
5:55 Petrobon sand, specific sand made for metal casting
Can you see the mistake I made with the mold?
8:15 Molten aluminum, degassed with sodium carbonate and fluxed with specific aluminum flux
9:40 Cut sprue with metal cutting band saw
10:11 Grind off flashing and flattening the back on the 2x72 belt grinder
10:35 Mark the center with a forstner bit wide as the shaft hole in the bottom
10:50 Drill the center hole, this is crucial for the wheel to run true
11:11 With my mistake in the pattern I had to carve out a bit of the back side to prevent the final dirll bit to go sidewat (drill bit move when cutting in one side only)
11:31 Final Forstner bit, rills accurate hole but it's meant for wood so it takes a while
12:00 Grind groove for seger with rotary tool
12:30 Grind groove for shaft key with rotary tool
12:59 Cut key channel in pulley with jigsaw, yep, it works!
13:35 Started to turn the wheel true with an angle grinder but it was too slow
14:00 A sharp chisel works way better
14:26 I found the best one was a small woodworking chisel with a very thin and sharp ege, I guess the less contact area the better it cuts
15:26 Checking for roundness. Good enough for my application!
I would suggest against turning the inside of the wheel by hand, it's a bit dangerous.
The mass of the wheel compared to the motor rotor for a motor as big as this does not count much for balance. I Checked the wheel for balance and was not able to find a "heavy" spot, so I did not drill any hole to balance the weight better. But yeah, that's was the plan!
Thanks a lot for watching, I hope you liked the video!
Suggestions and comments are welcome.
Leave a like and share to anyone who might be interested!
★Patreon★
https://www.patreon.com/blackbeardpro...
★Website★
http://blackbeardproject.com/
★Follow me★
Facebook ► https://www.facebook.com/BlackBeardPr...
Twitter ► https://twitter.com/BlackBeardProje
Instagram ► https://www.instagram.com/black_beard...
From Broken Pump To Belt Grinder Motor | Making A Drive Wheel WITHOUT Lathe camera iphone 8 plus apk | |
4,320 Likes | 4,320 Dislikes |
115,249 views views | 1.42M followers |
How-to & Style | Upload TimePublished on 18 Oct 2019 |
Không có nhận xét nào:
Đăng nhận xét